My key takeaways from attending the Lean School on Continuous Improvement at University of Kentucky’s TrueLean program
In 2018, the company I was working for decided to invest in training employees in Lean Management, based on the Toyota Lean Quality Management principles of Lean Manufacturing. The ultimate goal was to develop a learning organization that embraces continuous improvement. Developing a lean culture was important to our CEO and he brought in Jamie Flinchbaugh, an expert in the field of Lean to guide our lean journey.
Soon after, myself and 7 other employees were chosen to visit the University of Kentucky to attend the TrueLean program.
The training took place at UK in Lexington, Kentucky over several months. We attended week long sessions each month with students from other companies and industries. This created diverse new perspectives, an important piece of the Lean Systems Management puzzle.
Key Takeaways from My Lean Training: Problems are Good!
While there were so many tangible learning moments, one of the biggest aha moments for me was learning that problems are actually good.
Yep. That’s right.
It sounds so counterintuitive. Too often, problems are seen as mistakes and result in painful and punitive emotions and workplace tension.
But in a Lean culture, problems are seen as opportunities for continuous improvement and encouraged. In fact, companies who were further down the path in their adoption of Lean actually reported allocating company time for problem-solving. What a revelation!
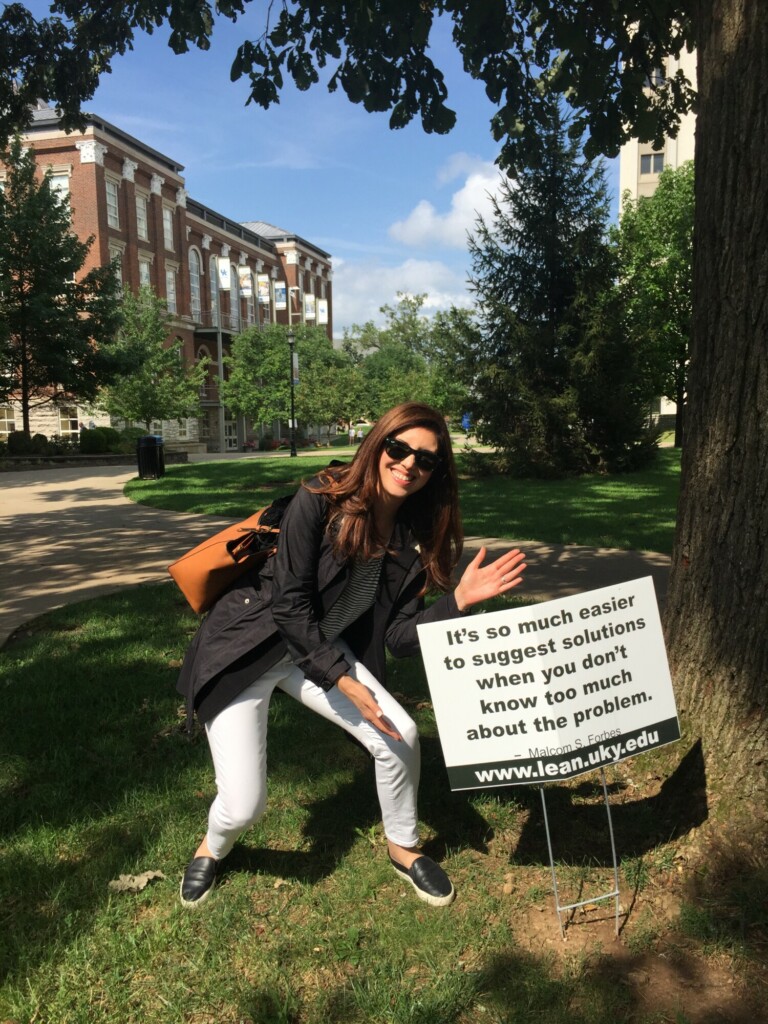
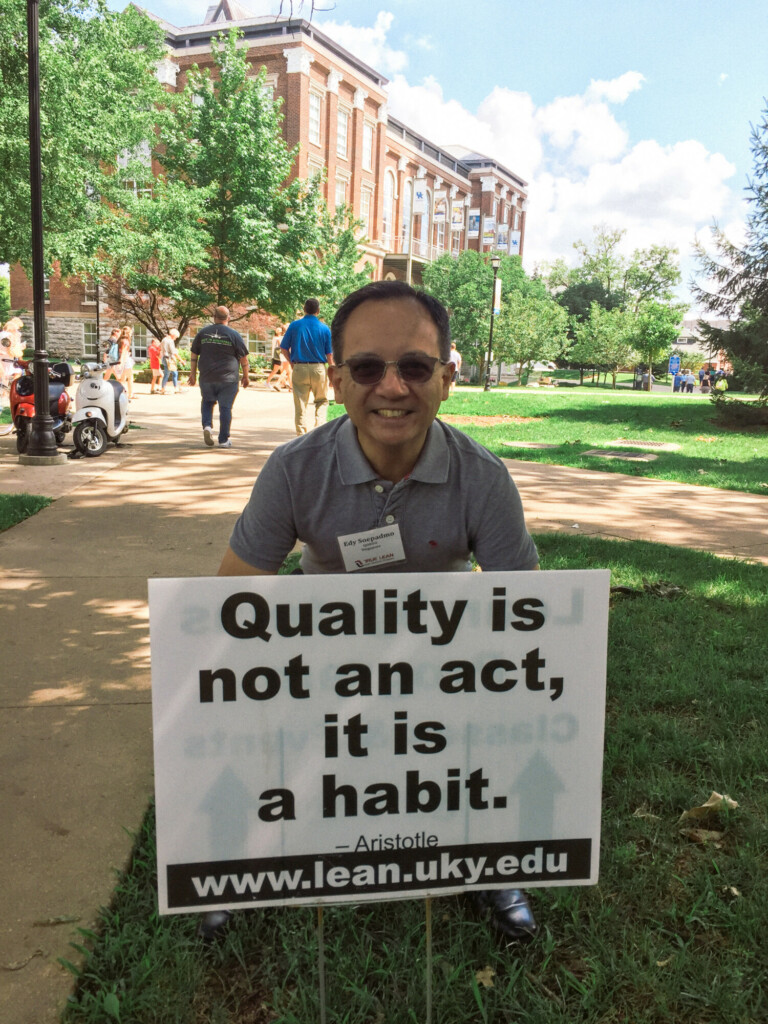
An 8-Step Lean Problem-Solving Technique
As part of the training, we applied our learning to real-world situations – both as a team and on an individual level. I identified a project, then applied systematic problem-solving techniques to make improvements.
Using the 8 step problem-solving technique, I used the following steps to make improvements:
Step 1. Clarify the Problem
Step 2. Break Down the Problem
Step 3. Target Setting
Step 4. Root Cause Analysis
Step 5. Develop Countermeasures
Step 6. See Countermeasures Through
Step 7. Monitor Both Results and Processes
Step 8. Standardize Successful Processes
PDCA = Plan, Do, Check, Act
This exercise allowed me to examine an actual problem in my workplace. After looking at the gaps and challenges, I was able to see more clearly where the issues were originating and create new processes that solved the problem. It was extremely helpful.
A Great Lean Tool for Learning (Try it!)
One of the key concepts behind Lean Systems Management is that this process is much more about behaviors than tools. It’s about integrating new learning into our everyday practice with a growth mindset.
That said, many of the tools are very helpful as well, and feed into our ability to recognize and adjust those growth-mindset behaviors. One of the tools that I love to use is the After Action Review (AAR). Similar to a post-mortem or debrief, it is a simple process of reflection. The four focal points of the AAR:
- Q1: What did we expect to happen?
- Q2: What actually happened?
- Q3: What can we learn?
- Q4: What can we do differently?
We don’t often take the time to identify gaps in expectation vs. reality, and as a result, learning opportunities can be missed. Using this tool creates a systematic approach to creating a learning moment from each experience. By asking these questions in a routine way, the learning becomes habitual and documented rather than merely anecdotal or accidental.
While I still struggle to make time for systematic problem-solving, I absolutely love Lean principles, concepts and practical tools for solving problems. It’s helped me reduce stress to know how to tackle problems and view them as opportunities – ultimately feeling more productive and purposeful in my work.
If you give the After Action Review process a try, I’d love to hear about it!
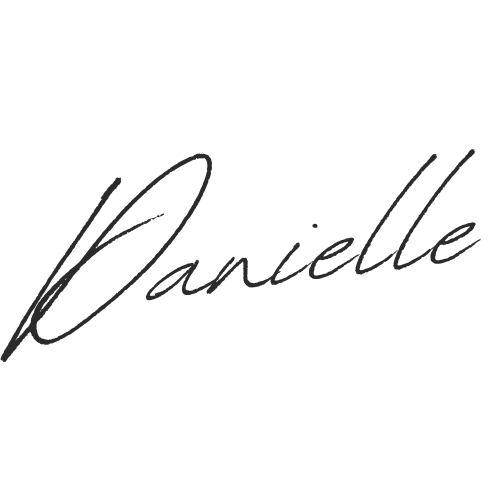